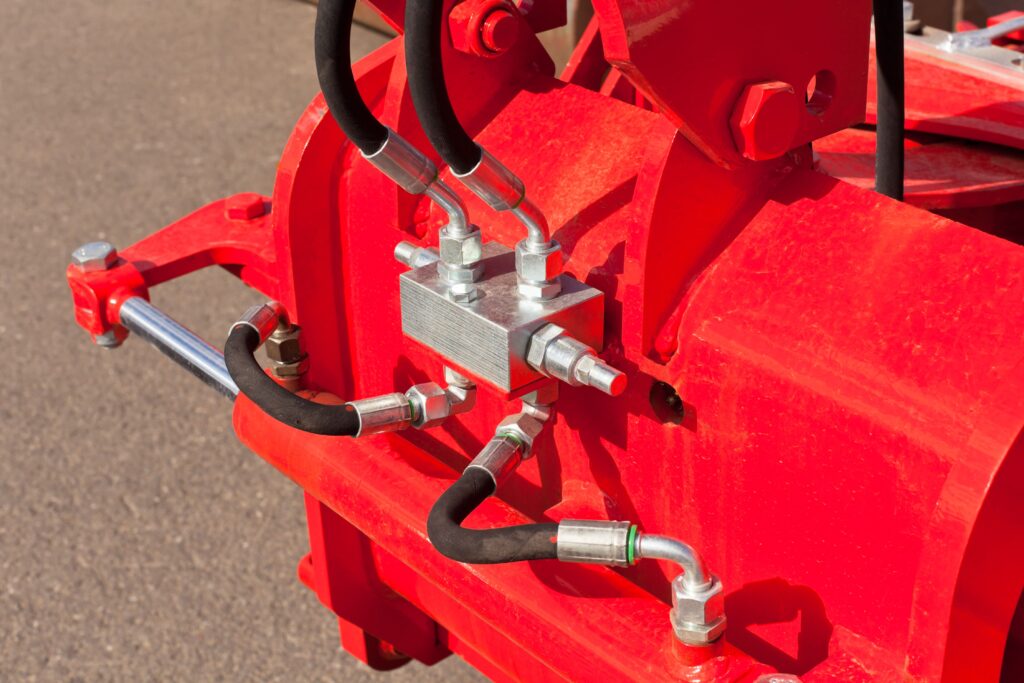
A hydraulic system uses fluid to transmit force and perform work. The core principle behind hydraulics is Pascal’s Law, which states that pressure applied to a confined fluid is transmitted equally in all directions. This allows the system to amplify force and control movements with precision, making it essential in machinery like construction equipment, vehicles, and industrial tools.
Main Components of a Hydraulic System
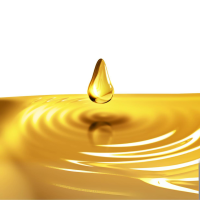
Hydraulic Fluid
This is the medium used to transfer force within the system. Hydraulic fluids are typically oil-based and are chosen for their ability to lubricate, resist compression, and transfer pressure effectively.
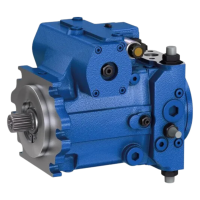
Pumps
Hydraulic pumps convert mechanical energy into hydraulic energy by creating pressure in the hydraulic fluid. They draw fluid from a reservoir and push it through the system.
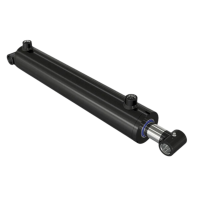
Actuators
Actuators, such as hydraulic cylinders or motors, convert hydraulic energy back into mechanical motion. They are responsible for tasks like lifting, pushing, or rotating.
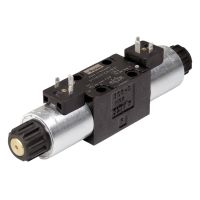
Valves
Hydraulic valves control the flow and direction of the hydraulic fluid. They regulate pressure and ensure that the fluid moves to the correct components, allowing for smooth and efficient operation.
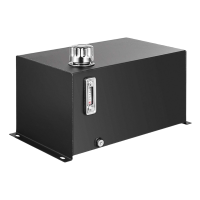
Reservoirs
The reservoir stores hydraulic fluid and helps maintain the system’s fluid levels. It also facilitates fluid cooling and filtration.
How Do Hydraulic Systems Work?
Hydraulic systems operate on a simple principle: Pascal’s Law, which states that when pressure is applied to a confined fluid, it is transmitted equally in all directions. Here’s how it works in practice:
1. Hydraulic Fluid
The hydraulic fluid, usually oil, is the lifeblood of the system. It transmits power, lubricates moving parts, dissipates heat, and helps remove contaminants to keep the system running smoothly.
2. Pumps
The hydraulic pump acts as the heart of the system, moving the fluid and generating the pressure needed to drive the system. Common types include gear pumps, vane pumps, and piston pumps.
3. Actuators (Cylinders and Motors)
Actuators convert the hydraulic fluid’s pressure into mechanical energy, which is used to move or lift objects. Cylinders create linear motion, while motors produce rotational motion.
4. Valves
Valves control the flow of hydraulic fluid, directing it to different parts of the system. They ensure that the fluid goes where it’s needed and at the right pressure.
5. Reservoirs
The reservoir stores the hydraulic fluid when it’s not in use, helps cool the fluid, and allows air to escape from the system. It ensures a steady supply of fluid and maintains system efficiency.
How to Maintain a Hydraulic System
Proper maintenance of a hydraulic system is essential for ensuring its reliability, efficiency, and longevity. Here are some key steps to keep your hydraulic system in top shape:
1. Regularly Check Hydraulic Fluid Levels
Maintaining the correct fluid level is crucial for smooth operation. Routinely check the reservoir and top off the fluid as needed to avoid low levels that can cause system damage.
2. Inspect and Replace Filters
Hydraulic filters remove contaminants from the fluid, preventing them from damaging the system. Regularly inspect and replace filters according to the manufacturer’s recommendations to keep the fluid clean.
3. Monitor Fluid Quality
Over time, hydraulic fluid can become contaminated or degrade. Periodically test the fluid for signs of wear, contamination, or degradation. If the fluid appears discolored or smells unusual, it’s time to replace it.
4. Inspect Hoses and Connections
Check hoses and connections for wear, cracks, or leaks. Damaged hoses or loose connections can lead to leaks and system failure, so replace any damaged components immediately.
5. Check for Leaks
Leaks can lead to fluid loss and reduced system efficiency. Regularly inspect the system for any signs of fluid leakage, especially around seals, fittings, and connections.
6. Monitor System Pressure
Proper system pressure is vital for optimal performance. Regularly monitor the pressure gauge to ensure it’s within the recommended range. If the pressure fluctuates, investigate and address the issue.
7. Keep the System Clean
Dirt and debris can cause contamination and damage to the system. Clean the exterior of the hydraulic system regularly, and make sure the area around it is free from dust and debris.
8. Follow Manufacturer’s Maintenance Schedule
Adhere to the manufacturer’s maintenance guidelines for inspections, fluid changes, and component replacements. This will help you avoid unexpected breakdowns and extend the life of the system.
9. Train Personnel on Proper Maintenance
Ensure that everyone involved in maintaining the hydraulic system is properly trained. This helps in performing maintenance tasks correctly and safely.
Summary
Keeping your hydraulic system in good shape is key to making sure it runs smoothly and lasts a long time. These systems are essential for powering everything from construction equipment to industrial tools. By regularly checking fluid levels, inspecting parts, and following the manufacturer’s maintenance tips, you can avoid unexpected issues and keep your machinery working efficiently. Whether you’re looking for hydraulic equipment, expert advice, or just want to learn more, we’ve got you covered. Contact us today to find out how we can support your projects with top-quality hydraulic solutions.